The API 653 standard governs most of the world's storage tank facilities, dictating inspection procedures. Facilities with API 650 or API 12C tanks are required by law to comply with API 653 inspection regulations.
One of the key inspection processes under API 653 is to take ultrasonic tank wall thickness measurements for the top, bottom, and sides of the tank. Completing this inspection for tanks 50ft or taller is dangerous, slow, and expensive. Read on to understand the current process, and how Skygauge Robotics offers a better way.
What is API 653?
The American Petroleum Institute's 653 standard covers maintenance, inspection, alteration, and repair of aboveground storage tanks built to the API 650 or API 12C standards. These tanks are generally over 50 feet tall and have a diameter greater than 30 feet, and meet a set of pre-defined dimensions outlined by API.
One of the requirements under the API 653 standard is regular ultrasonic spot thickness inspection of the bottom, shell, and roof of tanks to determine the minimum remaining thickness in these areas. When an inspector gathers this thickness data using ultrasound, it is compared to API's standards of minimum required thickness and maximum corrosion rate.
If, based on data from a series of tests over time, the wall is corroding faster than the maximum corrosion rate, repair or replacement of the asset is in order. If the wall is below he minimum required thickness, repair is required.
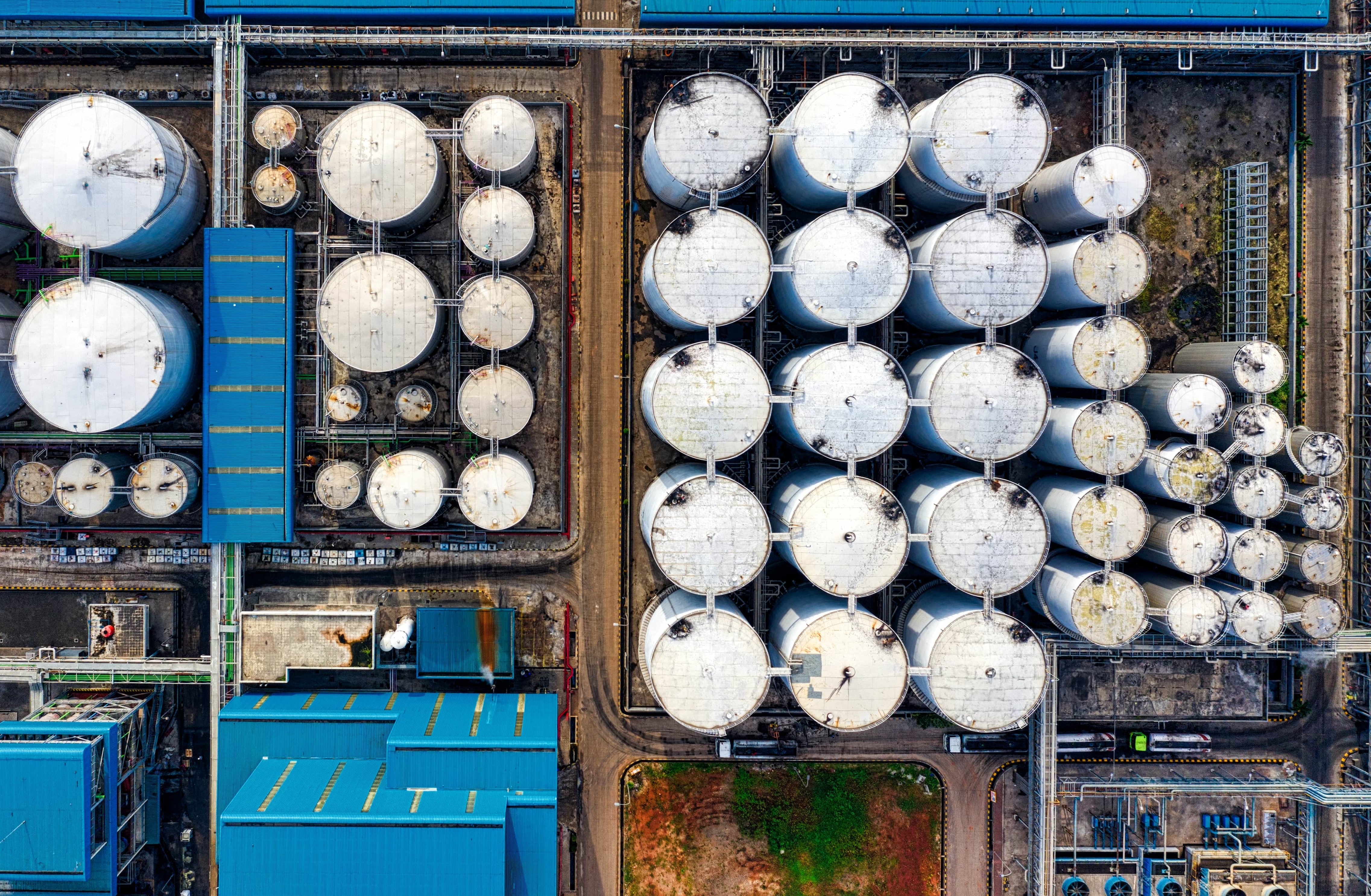
The Current Method
This is, by necessity, an approximation. Ideally, the asset owner would know the exact thickness of the steel at every point on the tank, at all times, but practically speaking we take a "snapshot" every 2 to 5 years. The inspector climbs the side of the tank using ropes, a crane, or scaffolding and takes readings on 40-60 points to get a reasonable approximation of the tank's overall condition.
At a rate of 6 points per hour, this process can take days or weeks for even a modestly sized tank terminal and requires manpower. The facility has to operate at a reduced capacity or go down completely for the duration of the inspection. Due to the large downtime and complexity of the process, it is not practical to do it more often then every couple years.
There is also a significant associated carbon footprint - scaffolding, man lift cranes, and the vehicles required to mobilize a large crew of inspectors are all emitters. Reducing this footprint with no impact on inspection quality can help facilities meet their emissions targets.
Inspection with Skygauge
The Skygauge is capable of conducting 60 spot thickness tests per hour, while the facility continues its day-to-day operations. It does not require an aerial work platform, and workers remain safe on the ground while the drone flies up to conduct the inspection.
The result is that asset owners can complete an API 653 compliant inspection in hours or days, rather than days or weeks, and can do so safer and easier than traditional methods.
There is little to no facility downtime, and the carbon footprint of a single crew and one electrically powered drone is negligible.
Another key factor is inspection frequency. Since inspections can now be done in a day or two with no downtime, regulators and asset owners can commit to a more frequent inspection cycle. This will give a more accurate snapshot of asset health over time, making it easier to comply with API 653 requirements. This means improved site safety for everyone because issues are caught and rectified faster, leading to fewer incidents and failures.
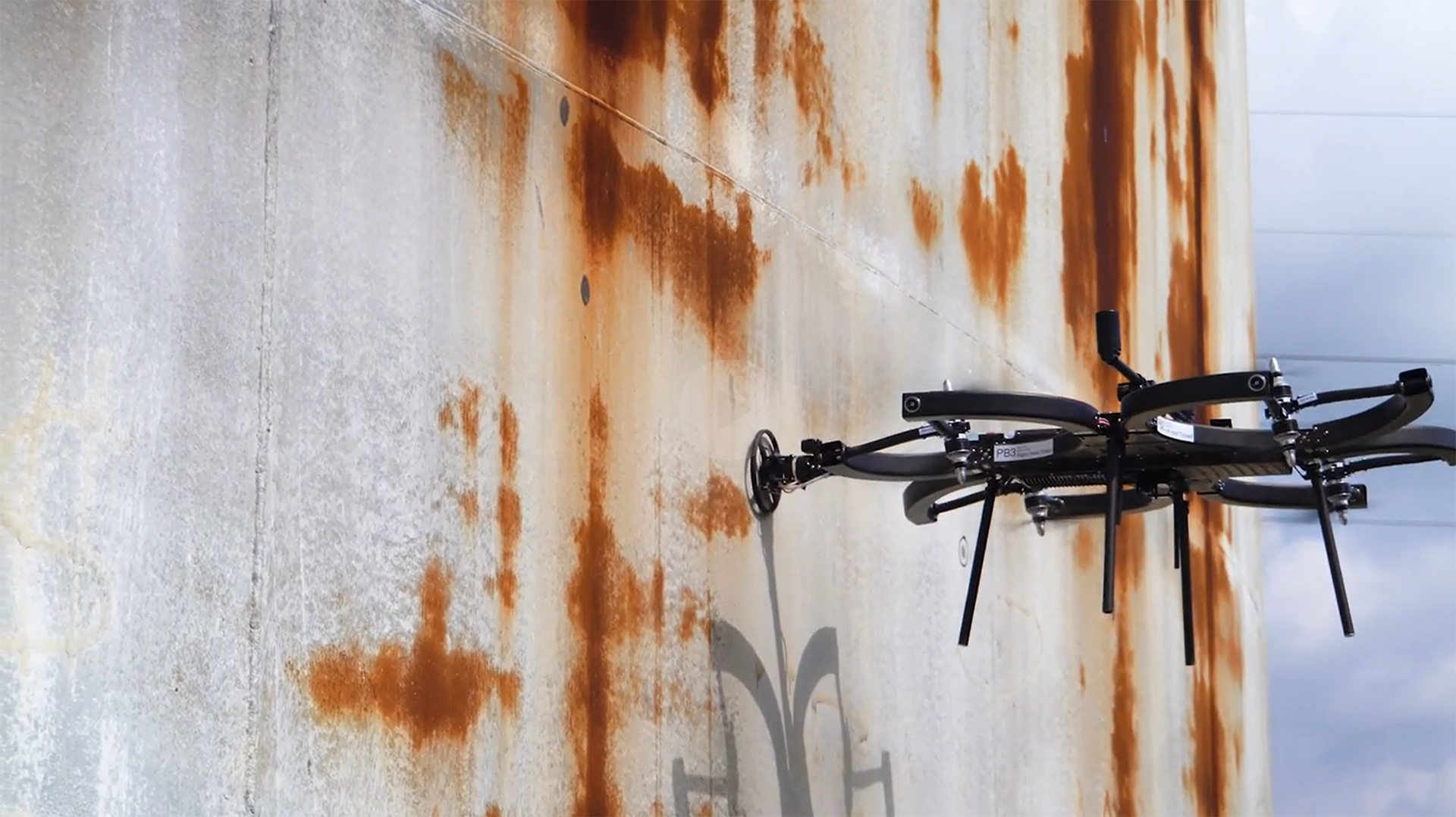
It also costs significantly less for inspection service providers to conduct a drone inspection. With savings of 50%-90% in cost and similar savings in terms of time, using a drone is a far better way to conduct API 653 inspections.
Similar to the way Skygauge is transforming ultrasonic inspections, drone technology has already begun to transform visual inspections. For instance, by adopting drone inspection services, the oil and gas industry has seen a 50% cost reduction for visual inspections. Inspections done by drone are cost-effective, and much safer than manual inspections.
Summary
API 653 inspections are faster, easier, and safer when done by a Skygauge Inspection Drone. Additionally, drones allow for more frequent inspections without sacrificing quality or increasing downtime. This allows for more timely data collection and better compliance with API's regulations.